Disposable Syringe Mold /mould
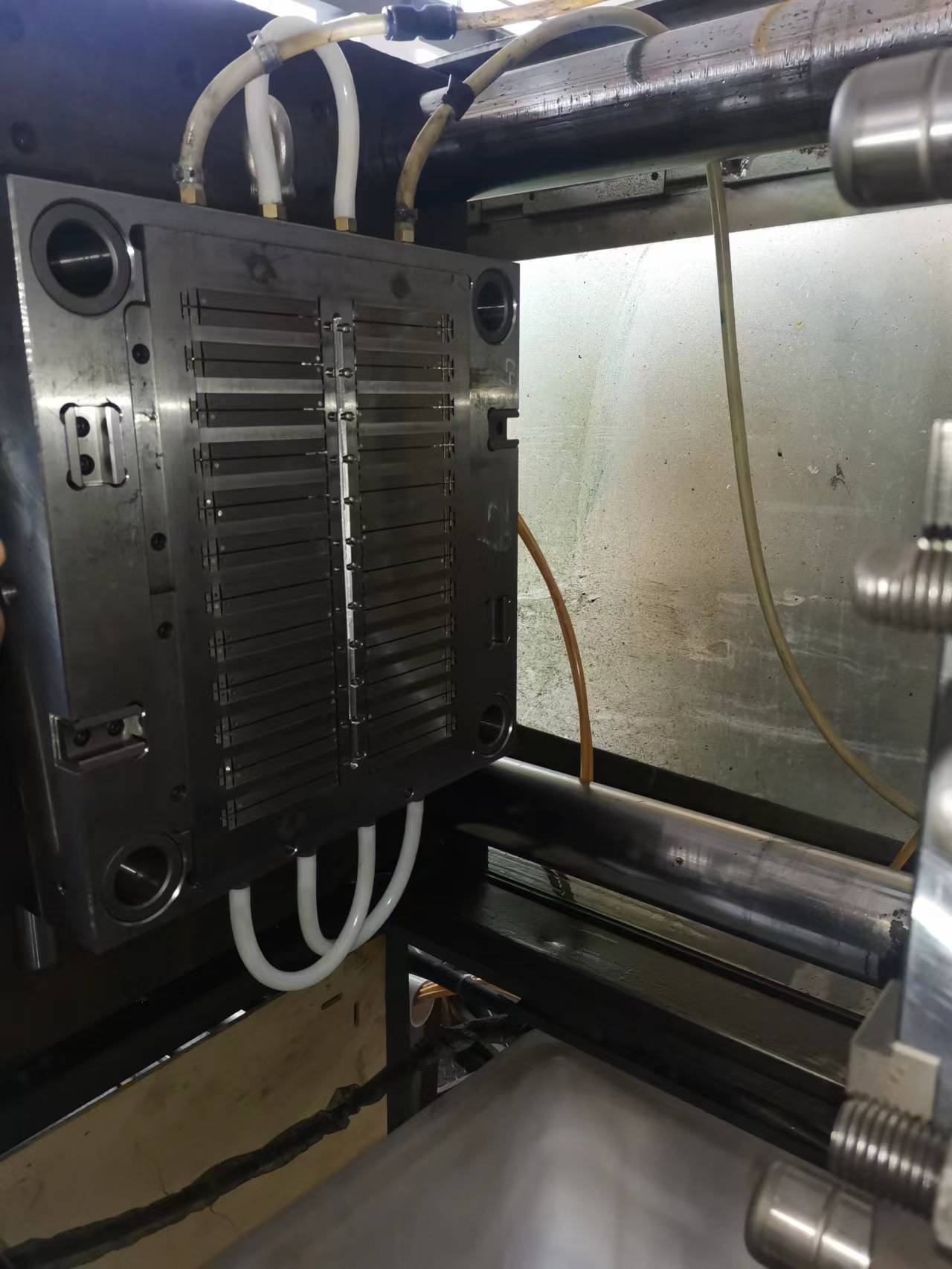
Disposable syringe molds are important tools used in the manufacturing process of disposable syringes, which are widely used in injection and infusion in the medical industry. Here are some key aspects of disposable syringe molds:
Mold Design: The mold for a disposable syringe is specifically designed to create the shape and features required for the syringe assembly. Typically, it consists of two halves, an injection mold and an ejection mold, which are combined to form a cavity. Molds are usually made of high-quality steel or aluminum to withstand the high pressure and temperature involved in the injection molding process.
Material Injection: The mold is prepared in an injection molding machine by heating the raw material (usually a medical-grade plastic such as polypropylene) until it reaches a molten state. The molten material is then injected into the mold cavity under high pressure. It flows through channels and gates within the mold, filling the cavity and forming the shape of the syringe assembly. The injection process is strictly controlled to ensure precision and consistency in syringe production.
Cooling, solidification and ejection: After the material is injected, the molten material cools and solidifies inside the mold. Cooling can be achieved by integrated cooling channels in the mold or by moving the mold into a cooling chamber. After solidification, the mold is opened and the finished syringe is ejected using a mechanism such as an ejector pin or air pressure to ensure safe and efficient removal from the mold.
Quality control measures are implemented throughout the manufacturing process to ensure that syringes meet required specifications and adhere to medical standards. This includes checking mold designs, monitoring injection parameters and post-production inspection of finished syringes to ensure their quality, functionality and safety.
Overall, disposable syringe molds enable mass production of disposable syringes, which plays a vital role in healthcare environments. The mold ensures that syringes are always produced to required specifications, meet medical standards, and provide reliable performance when used for injection or infusion.
1.R&D | We receive customer 3D drawing or sample with details requirements |
2.Negotiation | Confirm with clients details about: the cavity, runner, quality, price, material, delivery time, payment item, etc. |
3.Place an order | According your clients design or chooses our suggestion design. |
4. Mould | First We send mould design to customer approval before We make the mould and then start production. |
5. Sample | If the first sample come out is not satisfied customer, we modify the mould and until meet customers satisfactory. |
6. Delivery time | 35~45days |
Machine Name | Quantity ( pcs ) | The original country |
CNC | 5 | Japan/Taiwan |
EDM | 6 | Japan/China |
EDM ( Mirror) | 2 | Japan |
Wire Cutting ( fast ) | 8 | China |
Wire Cutting ( Middle ) | 1 | China |
Wire Cutting ( slow ) | 3 | Japan |
Grinding | 5 | China |
Drilling | 10 | China |
Lather | 3 | China |
Milling | 2 | China |